Welcome to the fascinating world of Harley-Davidson! We’re all familiar with the classic American rumble of a Harley, and the iconic design of the motorcycles. But have you ever wondered what percentage of Harley-Davidson motorcycles are made in the USA? In this article, we’ll dive into the history of Harley-Davidson and explore how much of the motorcycle production takes place stateside. So, hold on to your helmets and let’s get ready to ride!
Approximately 70-80% of Harley-Davidson components are manufactured in the USA, including major parts like engines and frames. Some components are sourced internationally.
Background of Harley-Davidson
Harley-Davidson ranks as one of the most iconic American motorcycle brands, and it has been a staple of the United States motor industry since it was founded back in 1903. Over the years, this brand has become synonymous with the biker culture, with its distinctive bikes and a loyal following of passionate riders.
This company was founded in Milwaukee, Wisconsin by William S. Harley and Arthur Davidson. The company had a humble beginning as the founders started producing bikes in a small shed in 1903, and it quickly gained a reputation for performance and quality. By the end of that decade, Harley-Davidson has already become the biggest motorcycle manufacturer, with dealerships all over the United States. Throughout the 20th century, Harley-Davidson continued innovating and expanding its production line. The bikes were also used in the United States military during the two world wars, solidifying the company’s place in American history.
Harley-Davidson has had a major impact on American culture, with its bikes becoming a huge symbol of freedom and individuality. The brand’s motorcycles are generally associated with rebelliousness and counterculture, with the riders sporting leather jackets and bandanas as a part of their biker attire.
Aside from its cultural impact, Harley-Davidson has also had a major economic impact in the United States. The company employs thousands of people from all over the country, with manufacturing facilities in numerous states, including Wisconsin, Pennsylvania, and Missouri. Harley-Davidson has also been a significant contributor to charitable causes and community organizations. The company’s charitable foundation has donated millions of dollars to organizations supporting education, health, and social services.
What Percentage of Harley-Davidson Parts are Made in the United States
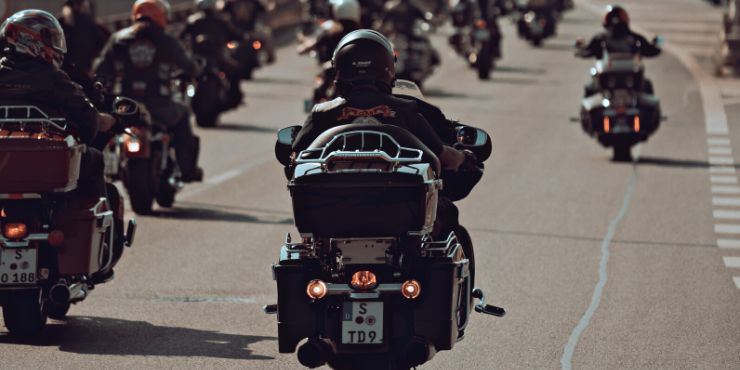
Harley-Davidson is a legendary brand that has been manufacturing bikes in the United States for more than 120 years. The brand’s commitment to quality and performance has made this an iconic brand that has been recognized all over the world. However, a large percentage of Harley-Davidson parts are still manufactured in the United States.
Before diving deeper into the numbers, it’ll be important to understand the complexity of the brand’s supply chain. Like many other motorcycle manufacturers, Harley-Davidson sources its parts and materials from all over the brand. Although individual parts might come from various countries around the world, the bikes are still assembled in the United States.
According to Harley-Davidson, the company sources most of its materials and parts from around 30 countries around the world. These parts and materials then get assembled into bikes at the company’s manufacturing facilities in the United States.
Given the complexity of Harley-Davidson’s supply chain, it can be pretty difficult to determine the exact percentage of parts that are manufactured in the United States. However, the company has also provided ample information on this topic.
According to Harley-Davidson, more than 70% of the total value of parts and materials used for producing each Harley-Davidson bike is sourced from within the United States. This means that most of the value of each Harley-Davidson bike comes from materials and parts that are produced in the United States. It is important to note that this percentage might vary depending on the specific model of your Harley-Davidson bike. For instance, some models might have a higher percentage of parts that are made in the United States than others.
Despite the complexity of Harley-Davidson’s supply chain, the company still remains committed to domestic production. The company has various manufacturing facilities in the United States, including facilities in Pennsylvania, Wisconsin, and Missouri. Recently, the brand has also invested heavily in new technologies and processes that have helped improve the company’s domestic production capabilities.
Manufacturing Process of Harley-Davidson Bikes
Harley-Davidson is a huge motorcycle brand, arguably the biggest and most historic motorcycle brand in the United States motorcycle industry. The brand’s manufacturing process is steeped in tradition and craftsmanship, with each bike being carefully handcrafted by skilled technicians and large machines capable of churning out high-quality components. Here is the manufacturing process involved in the production of Harley-Davidson motorcycles.
1. Design and engineering
The manufacturing process of Harley-Davidson bikes starts with the design and engineering of the bike. The design team of Harley-Davidson works closely with technicians and engineers to develop a prototype that meets the brand’s high standards for quality, style, and performance. Once the design has been finalized, the engineering team makes use of computer-aided design (CAD) software for creating 3D models of the bike’s components. These models will then be used for creating molds and tooling for the manufacturing process.
2. Sourcing raw materials
The next step in the process to manufacture a Harley-Davidson bike involves the sourcing of raw materials. Harley-Davidson makes use of a wide variety of materials for producing its bikes, including aluminum, steel, and chrome. The brand sources these materials from domestic suppliers, making sure that the motorcycles are made using the highest-quality materials available in the market.
3. Manufacturing
The actual manufacturing part of this process will begin with the frame. Harley-Davidson frames are made using high-quality steel. Each frame is then carefully welded manually to make sure it gets the strength and durability Harley-Davidson is renowned for.
Once the frame gets completed, the technicians and engineers add other components, including the engine, transmission, suspension, wheels, and more. Each component is inspected carefully to ensure that it meets the high standards for quality and performance that Harley-Davidson is known for.
4. Assembly
The final step in the manufacturing process involves the assembly of the Harley-Davidson motorcycle. Each motorcycle is carefully hand-assembled by skillful experts and technicians who take great pride in their work. The assembly process will include the installation of the fuel tank, seat, handlebars, and other components.
Once the Harley-Davidson motorcycle is fully assembled, it will undergo a rigorous quality control inspection to make sure that it meets the brand’s high standards for safety, quality, and performance.
Challenges of Domestic Production
For over a century, Harley-Davidson has been producing world-class motorcycles in not just the United States, but all over the world. While the iconic company has a rich history and a loyal customer base, it does face many challenges when it comes to domestic production. Here are some of the challenges that Harley-Davidson faces in terms of the domestic production of bikes in the United States –Â
1. Access to skilled labor
One of the biggest challenges that the brand faces in the domestic production of its bikes is access to skilled labor. The cost of labor in the United States is generally higher than compared in other countries, which can make it quite difficult for the company to compete on price. Additionally, the cost of benefits such as healthcare and retirement plans can significantly add to the cost of labor.
For addressing this challenge, Harley-Davidson has implemented numerous strategies to improve efficiency and reduce costs. For example, Harley has invested handsomely in new technologies and processes that have helped streamline production and reduce waste. Additionally, the company has also worked smartly to improve its supply chain and reduce the cost of materials.
2. Competition from foreign manufacturers
Another challenge that the company faces in domestic production is competition from foreign manufacturers. Recently, foreign manufacturers like Yamaha, Honda, and Kawasaki have entered the US market, and they’ve been offering bikes at lower prices compared to Harleys.
To remain competitive, Harley-Davidson has focused on improving the quality and performance of its bikes. The brand has also invested in new technologies while also working on improving the efficiency of its production processes. Additionally, the brand has also expanded its product line to include new models from different lineups, while also focusing on marketing to a broader audience.
3. Cost of materials
Another challenge that Harley-Davidson’s domestic production faces is the cost of materials. The brand relies on a wide network of suppliers and partners to produce the raw materials, components, and services required for producing different components. Moreover, coordinating this network can end up being a major challenge. The brand also makes use of high-quality raw materials to make sure it delivers the best quality that the company is known for.
Harley-Davidson has worked on mitigating this challenge by building strong relationships with the suppliers and partners with its suppliers and partners. Further, the company has also invested in technology and process to help improve supply chain visibility and lower the cost of materials. This way, the brand can maintain a robust quality control program for ensuring that it meets the high standards for quality and performance.
4. Regulatory compliance
Domestic production in the United States is subject to a web of federal, state, and local regulations. Complying with all these regulations can be quite a challenge for Harley-Davidson. The company needs to comply with a wide range of safety, environmental, and labor regulations among others. Failing to comply with these laws will result in files, lawsuits, and damage to the brand’s reputation.
For addressing this challenge, Harley-Davidson has established strong internal compliance programs while also working closely with government regulators for ensuring that its operations meet the applicable laws and regulations. The brand also invests in training and education programs to help the employees understand and comply with regulatory requirements.
Benefits of Domestic Production
Harley-Davidson’s commitment to domestic production has a wide range of benefits, both for the company and the American economy as a whole. Here are some of the benefits that domestic production of Harley-Davidson bikes brings to the table –Â
1. Creating jobs locally
One of the most significant benefits of Harley-Davidson’s domestic production is job creation. By producing bikes in the United States, the brand can create jobs for American workers. These jobs range from skilled manufacturing and position as engineers, technicians, and more to administrative and support staff.
According to Harley-Davidson, the company employs more than 5,000 in the United States. Most of these jobs are located in Wisconsin, where the brand is headquartered. Aside from these direct jobs, Harley-Davidson’s domestic production will also create indirect jobs in related industries like retail, transportation, and logistics.
2. Support of local economy
Besides job creation, Harley-Davidson’s domestic production also has a significant impact on the local economy. The brand’s operations generate billions of dollars in economic activity each year, both locally and nationwide, both through direct spending and through the ripple effects of its supply chain.
In fact, according to a study conducted by the University of Wisconsin-Madison, the company’s economic impact in Wisconsin alone is estimated to be more than $3 billion annually. This doesn’t just include direct spending by the company and the impact of its supply chain and the spending of its employees.
3. Quality control
Another huge benefit of the domestic production of Harley-Davidson is the brand’s ability to maintain strict quality control standards. By producing the production of bikes in the United States, the iconic brand can closely monitor the manufacturing process and make sure that every single model produced meets high standards for quality and performance.
The company has a reputation for producing some of the highest quality bikes in the world. Harley’s commitment to domestic production plays a major role in maintaining this reputation. By controlling the entire manufacturing process, from design to manufacturing to production to testing, the historic company can ensure that every single bike is built to its exact specifications.
4. Innovation and technology
Lastly, the company’s domestic production allows it to remain at the forefront of innovation and technology in the motorcycle industry. By investing in the latest technologies and processes, the company can improve the quality and performance of its bikes continuously.
Harley-Davidson has a long history of innovation and bringing revolutionary features to the forefront, from the introduction of the first-ever V-twin engine in 1909 to the development of its latest line of electric bikes recently. By producing motorcycles in the United States, the brand can continue this tradition of innovation and technology while also maintaining its position as the leader in the motorcycle industry.
What Does the Future Hold for Harley-Davidson Bikes?
Harley-Davidson continues to be a massive player in the United States motorcycle community, with a loyal user base and a commitment to sustainability and innovation. For decades, Harley-Davidson was known for sticking to the tradition and heritage of having huge bikes capable of delivering a powerful and comfortable riding experience. However, recently, the company has shifted its ideology and delved into other categories as well, releasing electric motorcycles like the LiveWire, environmental-friendly bikes, trikes, and more.
In the coming years, the brand is expected to release many new and exciting models in the coming months and years. In fact, Jochen Zeitz, the CEO of Harley-Davidson has claimed that the company is slowly transitioning to become an all-electric brand and this process may take decades. He says that at some point in time, Harley-Davidson will become an all-electric brand. Adding that this is a long-term transition that needs to happen, it isn’t something that can be done overnight.
According to Jochen Zeitz, electrification of the bikes is the only logical step in the evolution of Harley-Davidson, a company that has been at the top for last century or so. He says that looking at the past 120 years, the company has always evolved and never stood still. Just like the brand’s founders did back in the day by trying to invent something entirely unique, this is definitely something that the company will be doing now as well.
He added that what they’re doing here is celebrating the past, but also evolving the brand at the same time. It is the natural evolution that has to happen. Even though the company has already started to manufacture electric motorcycles, Jochen Zeitz doesn’t believe that the brand will be moving away from petrol-powered bikes in the near future.
Conclusion: The Final Verdict
The manufacturing process of Harley-Davidson motorcycles in the United States is a complex and skillful process that involves the use of high-quality materials, advanced technology, and the expertise of skilled technicians and engineers. The result is a beautiful bike that isn’t just a work of art, but also a testament to American craftsmanship and ingenuity. Most of the Harley-Davidson bikes are manufactured in the United States. In fact, the products are produced in factories all over the world and assembled to create a Harley-Davidson masterpiece in the United States.
The company has a commitment to domestic production in the United States, and it brings both challenges and benefits. Various challenges faced by the iconic motorcycle company involve the cost of labor, cost of materials, competition from foreign manufacturers, regulatory compliance, and more. Interestingly, the brand’s production domestically also has numerous benefits, both for the company and for the American economy as a whole. From job creation and economic impact to quality control and innovation, Harley-Davidson’s domestic production is a key factor in the company’s success and its status as an American icon. As Harley-Davidson continues to evolve and innovate, its commitment to domestic production will undoubtedly remain a cornerstone of its business strategy.
FAQs
How much of Harley Davidson’s parts are made in the US?
Harley Davidson sources components from a variety of suppliers around the world, but the majority of parts used in its motorcycles are made in the US. Approximately 70-80% of the parts used in Harley Davidson’s motorcycles are manufactured in the US.
Where are Harley Davidson’s motorcycles assembled?
Harley Davidson’s motorcycles are assembled at the company’s facilities in York, Pennsylvania and Menomonee Falls, Wisconsin. At these locations, parts from various suppliers are put together to create Harley Davidson’s iconic motorcycles.
What other countries are involved in the production of Harley Davidson motorcycles?
In addition to US-based suppliers, Harley Davidson also sources parts from suppliers in Japan, China, India, and Europe. These parts are then shipped to the company’s US-based assembly plants, where the motorcycles are put together.